WLC reveals the true costs of CHP
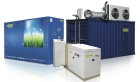
Given an adequate demand for heat, the ‘free’ electricity generated by a combined-heat-and-power installation makes a very powerful whole-life-cost argument. Marcus Dodsworth of Shenton Group explains.
The continuing and unwavering increase in energy prices together with ongoing legislation regarding carbon emissions has put energy management on the boardroom agenda. These unrelenting hikes in fuel costs and the need for clean, efficient and economic energy has put combined heat and power (CHP) into the limelight, with many managers and directors now considering it as a viable alternative to purchasing electricity from energy companies.
CHP or co-generation is the simultaneous production of electricity and heat from a single fuel source. A CHP system recovers the heat normally lost in electricity generation for use on site in space heating, domestic hot water, swimming pools or process heating. Compared with separate generation of electricity and heat, CHP systems can operate at more than 95 %efficiency.
CHP is ideal for any building where there is a demand for heat
The main benefit of a CHP system is that the overall annual energy costs can be reduced.
On site generation reduces the amount of electricity that has to be purchased from the grid. Although there will be a shift in gas/electricity balance of a building’s total fossil-fuel consumption, any rise in gas costs will be more than offset by the savings in electricity costs. Many buildings often have sufficient demand for space heating and hot water to utilise a small CHP plant. CHP providers can synchronise multiple units together to create a very efficient on-site power station that can substantially reduce electricity bills.
Whole-life costing (WLC) is an economic evaluation technique that encompasses the total cost of an asset over its operational life including initial capital costs, maintenance costs, operating costs and disposal costs. These projected costs achieve defined levels of performance that are required during the lifetime of a capital asset including reliability, safety and availability. WLC is an effective tool for considering the following.
• business justification
• procurement strategy
• concept approval
• investment decision
• readiness for service
• benefits/cost evaluation
WLC encourages companies to look beyond the upfront capital costs to take a long-term view of other important factors such as energy emissions. It also helps managers determine the full benefits of investing in CHP. When carrying out such an exercise it is important to take into account capital expenditure as well as all operating and fuel costs.
It is important to size the CHP system correctly to take into consideration the expected energy demands. Oversized CHP units fail to achieve the anticipated savings and have to dump or transfer heat energy or run at lower capacity. Undersized units miss out on potential savings. If your building has a heat load for at least 4000 h per year, then CHP could generate a substantial amount of free electricity while meeting this heat demand.
Remote monitoring of CHP systems allows maintenance to be carried out before any problems arise. Maintenance programmes specifically designed for CHP systems include Shenton Group’s Infinium24 that constantly renovates and re-engineers components before their projected replacement date. The ethos behind such programmes is to provide CHP users with a fixed, ongoing cost of ownership paid for by the savings made during the maintenance programme. The ability of knowing these costs upfront enables maintenance to be calculated within the whole-life costing of the CHP system.
Other advantages that need to be taken into consideration when calculating whole-life costings include the following.
• 95% efficient means less money spent on energy
• located on site means no transmission losses — what you generate is yours to use
• gas used can be exempt from the Climate Change Levy (CCL)
• reduction in use of existing boilers
• standby power facility
Although capital costs of CHP equipment are higher than conventional boiler plant, the equipment usually has lower whole-life cost when the annual expenditure on operation, maintenance, heating, ventilation and air conditioning as well as fuel costs become part of the equation. When reviewing the whole-life costings of CHP the following points need to be considered.
• comparison of the conventional provision of heat and power by boiler and electricity purchased from the local electricity network
• size of distribution for each building
• size of the CHP plant that is appropriate for each building size and type based on heat demand and by optimising the combined cost of heat and power supply
• assessment of the capital and service costs associated with operation of the CHP plant and assessing the cost effectiveness based on gas and electricity prices and projected increases in these costs
• calculation of the potential income from exporting excess electricity to the grid
• calculation of the primary energy saving from the CHP capacity in accordance with EU Guidelines
CHP is not a single technology, but an integrated energy system that can be modified depending upon the needs of the energy end user. CHP can use a variety of fuels to provide reliable electricity, mechanical power or thermal energy for industrial plants, universities, hospitals or commercial buildings — wherever power and heat are needed.
Whole-life costing enables a company to assess the cost of CHP throughout its entire life cycle. Using that insight allows CHP providers to optimise the design to minimise the total lifetime cost. The analysis of whole-life costs is also a key driver in enhancing organisational sustainability — both directly through reduced energy costs usage and waste, and by establishing an explicit framework for lifetime review against which sustainability can be assessed.
Marcus Dodsworth is technical service division manager with Shenton Group.